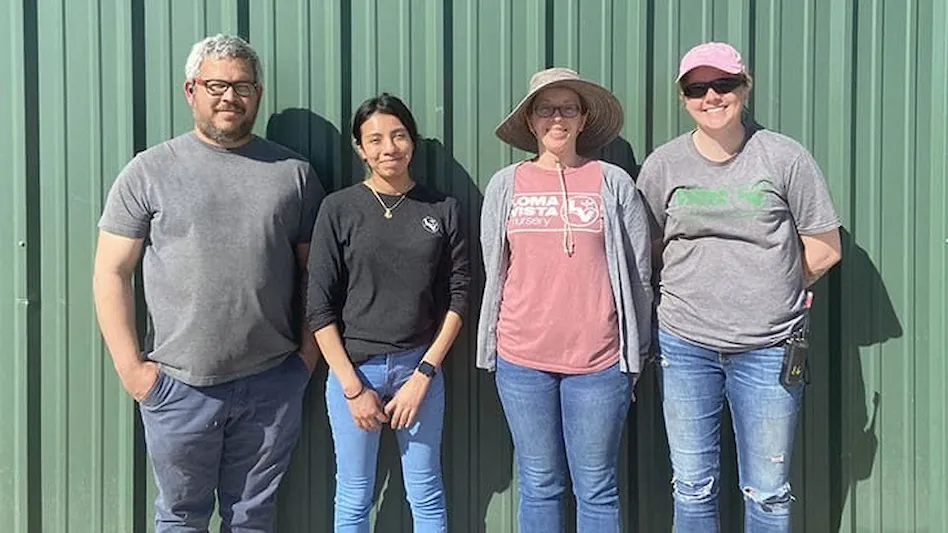
Loma Vista Nursery

Everyone knows there are rules from OSHA and WPS that growers must abide by. But simply abiding by the rules is not enough. Nor does it give anyone on the team reason to engage.
Going the extra mile by prioritizing safety as part of a daily coaching and reinforcement program — along with training and education — is a “win” that everyone can get behind. Why? Because a culture of safe behavior is a victory for the company’s brand, workforce and bottom line. In fact, it is a profit center.
When woven into the fabric of the nursery’s culture, “safety” means that every member of the team goes home in the same condition they arrived. It also means that everyone is working toward the common goal of bringing people together and growing the business.
As nursery owners, one of our many jobs is to protect the assets and investments of our company — No. 1 being our people. Therefore, it is our job to “sell safety” as part of a company-wide coaching program. I cannot stress enough that owner and supervisor investment in the program is critical. Without their complete commitment, a safety coaching program will not be successful.
Teams function best when they are set up for success. Members know the rules and how the score is kept. This very easily applies to employee participation in an internal safety program that daily defines leadership and individual responsibilities, explains how performance is measured and offers an incentive, a way to win.
The result is invested employees who look out for one another and the company’s best interests. Team members are incentivized by safety breakfasts that recognize staff and a semi-annual bonus that rewards safe practices.
We have learned a few things along the way.
Safe work, greater effectiveness
A healthy workplace begets a healthy workforce that supports a healthy bottom line. Unsafe work conditions and lack of attention to workplace safety causes undue stress. A safe work environment and positive safety culture are primary elements of an employee engagement and retention plan.
Safe work environments inspire confidence in the company’s leadership and reinforce its commitment to employees. The nursery is then a desirable place to work that attracts and retains top talent.
Creating a culture around safety increases efficiency and reduces expenses. The cost of a workplace accident is lost time in worker productivity and grower efficiency. It is also a direct hit to workers’ compensation insurance.
Prioritizing safety and implementing an effective workplace strategy can lower a nursery’s experience modification rating (or MOD score), which is used to price workers’ compensation insurance premiums. Loma Vista Nursery’s goal is a MOD score of under 1. That saves us about 20% annually on our workers’ comp policy.
Any decrease in expenses is an increase to the bottom line. For example, consider if a nursery’s net profit is 10 percent. A $5,000 savings (like the one that might result from implementing an effective safety program and achieving a lower MOD score) gives the company the same financial benefit, or profit, as $50,000 in additional sales revenue.
Coach safety, reinforce safe behaviors
We learned from our risk control partner, IMA, that 80 to 85 percent of all workplace safety-related incidents are the result of unsafe acts. Between 15 and 20 percent are the result of unsafe conditions. The numbers point out that developing a safety culture is way more important than doing safety walkthroughs to find “things” to fix. The stats also make a few points pretty clear.
First, leadership and employees must claim joint responsibility for team safety on the job. Second, individuals control their personal behavior. Third, coaching for safe behavior coupled with reinforcement is vital to a successful workplace safety program.
Staying vigilant about workplace structural issues helps avoid accidents. Positive reinforcement of safe behavior is at least equal to and perhaps more effective than education and training alone.
What causes people to change unsafe behavior? Coaching to reinforce safe choices. But even the best education and training program will fail without the coaching and reinforcement model being followed.
When we relied solely on education and training at Loma Vista Nursery, we did not get results. Coaching for safety — and reinforcing safe behaviors while correcting unsafe choices – is how we got great results. Coaching gets to the culture of the matter because developing a culture of safety prevents unsafe acts.
IMA, a national company with satellite offices throughout the country, empowered us to understand safety at Loma Vista Nursery. They helped us identify what we are doing well and where we could improve. Then, they supplied tools to support our program’s success.
They gave us access to the IMA Risk Management Center, where the company hosts hundreds of educational webinars, documents, and management and frontline training videos. The center provides scheduled training opportunities and use-reporting. Just like everything else in our business, our safety program must be documented so we have a record of what happened and we can measure our performance.

Incentivize safe behaviors
Offering modified duty when a team member is injured is an important part of our risk control strategy. However, promoting and incentivizing safe behaviors limits this need.
Through the constructs of our coaching program, each team member claims responsibility for their personal safety. Supervisors oversee the safety of all employees who report to them. Our safety committee meets regularly and includes frontline employees, supervisors and managers representing every department on the nursery.
The committee is responsible for investigating incidents as they occur. They evaluate conditions at regular intervals, and immediately address concerns and make needed repairs. Reporting, documentation and corrective measures have assignable action items and deadlines.
A positive safety culture empowers supervisors and frontline employees to report unsafe behaviors. Staff at all levels are more likely to do this when they know safety is a priority to leadership. Providing supervisors with the tools they need – and requiring them to use them as part of their job – helps them recognize safe and unsafe behaviors and coach team members successfully.
Coaching is what changes behavior and shapes culture on our nursery. When a supervisor or manager makes time to approach a team member to positively reinforce a correct safety behavior, that team member begins to understand the importance of the choice they made to work safely. Every day, our leadership has to prove that we are committed to safety and that it is a priority. Then, it is our job to help our supervisors and team members make it a priority as well.
Supervisor safety observation cards support our commitment to zero accidents. This required part of the supervisory role has transformed safety on our nursery because our team members communicate daily and document behaviors. Supervisors are given a quota of cards to complete. They are awarded bonuses for meeting goals. The beauty of this is that supervisors have a reason to either give positive reinforcement or correct unsafe behavior.
Using the cards, supervisors make observations, immediately coach employees who may be working in an unsafe manner and provide positive reinforcement when they spot a team member doing things right. Providing feedback and encouragement supports team member growth and inspires behavioral change.
The observation cards additionally provide historical data that informs staff coaching. For example, we had past incidents of back injuries due to improper lifting. So, safe lifting is a topic we coach on often and put policies around. When supervisors see team members using safe lifting, they provide positive reinforcement. If they see improper lifting, they immediately provide coaching to correct issues before injuries occur.
Coaching for the win
Our safety program addresses how to safely operate equipment across all departments. Training and education happen during our safety tailgate meetings. Coaching takes training and education a step further by providing positive reinforcement as team members go about their workday. That cements safe behavior and safe choices and corrects unsafe behaviors as they are observed on the nursery.
Operators are first educated, trained and certified. Then, coaching steps in to provide positive reinforcement and correct unsafe behaviors when team members are executing the responsibilities of their job. For example, we educate and train about how and why to use a seatbelt when operating a tractor. Coaching in the field takes that a step further by reinforcing safe behavior. It acknowledges operators for using the seat belt correctly and reminds them when they are not. We provide operators with detailed training for every tool they are certified to use, including maintenance protocols to keep equipment running at optimum performance.
It includes modeling correct ways of wearing personal protective equipment. Our coaching program outlines procedures for safely operating machinery, from gas-powered sheers and GreenElf fertilizer dispensers to tractors and skid loaders. Every employee operating equipment must complete our in-house certification program. At the conclusion, operators receive a safety vest.
This is a visual signal to management that employees operating our equipment have the tools and knowledge they need to work in a safe manner. This also means the likelihood of having a “good excuse” for operating equipment in an unsafe manner is slim.
Just like everything else in business, growing a safety culture on the nursery requires planning, on-going evaluation and adjustments. It’s not something you can “set and forget.”
Working safely is at the core of Loma Vista Nursery’s planning process and is backed by commitment at every level of the company. Our annual budget contains line items for safety bonuses, workers’ comp insurance, personal protective equipment and team member recognition.
If we have incidents that occurred in a prior year, we plan for ways to improve in the current year. We adjust infrastructure accordingly when warranted.
A good example of this is our heat stress safety training, which is OSHA-required. During hot Kansas summers, we adjust hours to start earlier so we can get outdoor work done before the day’s temperatures rise. We further scaled our education to provide employees with the early warning signs of heat-related illness, and prevention techniques centered on healthy eating and hydration.
It is hard to quantify the savings of our safety culture. But even more difficult would be quantifying the cost of a significant safety incident on the nursery.
Safety is an investment in the nursery’s people and its bottom line. With an efficient program in place, developing a culture of coaching and reinforcement is a “win” that everyone can get behind.


Explore the April 2022 Issue
Check out more from this issue and find your next story to read.
Latest from Nursery Management
- Redesigning the product and process
- GS1 US Celebrates 50-Year Barcode 'Scanniversary' and Heralds Next-Generation Barcode to Support Modern Commerce
- University of Florida offers Greenhouse Training Online program on irrigation water
- Tree Fund announces scholarship and spring cycle grant awardees
- ‘Part of our story’
- Asimina triloba
- Oregon Association of Nurseries announces death of Jolly Krautmann
- Dramm introduces new hose, sprinkler attachments for home gardeners, nurseries